Everyone loves a good bargain. Everyone’s eyes light up when find a new brand selling great clothes for a cheap price.
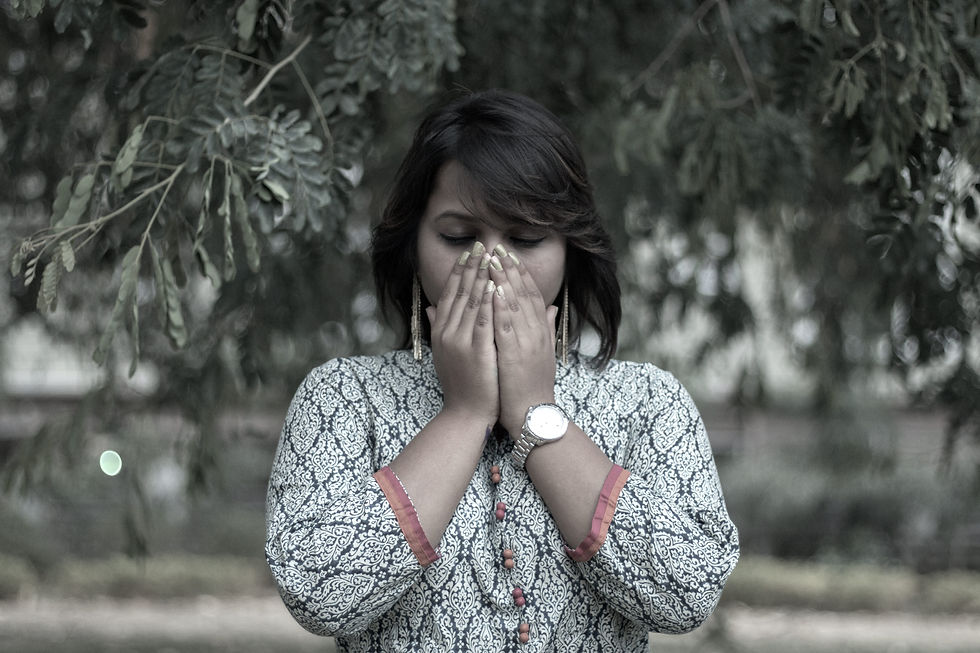
However, while you’re paying a low monetary price for new additions to your wardrobe, it’s likely that you’re playing a massive ethical cost.
The many tired supply chain in the apparel industry can generally be categorised into five main networks:
Raw material network(farmers & factories)
Intermediate goods network( textile plants/companies)
Production network ( garment manufacturers – companies and outsourced individuals)
Export network(textile companies / shipping companies)
Marketing network(distribution channels)
Each step in the apparel supply chain network has top countries that produce textiles the cheapest. That being said, according to 2013 data by the United Nations Commodity Trade Statistics, the largest textile exporters and at the same time the top cheapest producers include: China (USD 274 billion), India (USD 40 billion), Bangladesh (USD 28 billion), Pakistan (USD 27 Billion) and Indonesia (USD 12.3 Billion)
Challenges of Producing Cheap Textiles
Poor Pay
In most cases, garment workers in cheap textile producing countries are paid below minimum wage (based on the county in question). The minimum wage is often not enough for food, shelter, clothing or children’s education.
For example, monthly wages in Bangladesh, including compulsory overtime of between 51-125 hours a month, is valued at between USD 22 and USD 55. In Vietnam the monthly wage is between USD 21 and USD 50.
Since it is women that mostly have the skills that garment employers look for, they therefore constitute the largest population in the garment industry. They are also mostly employed because they are often paid less due to gender discrimination.
A lot of garment workers are also paid late and when paid, they often sign blank sheets which means that employers often misrepresent the wage bill to the government, therefore hiding the extent of the problem.
Irregular work and Job Uncertainty
Since the industry is extremely competitive, when orders are moved to different destinations, then garment workers easily lose their jobs. Additionally, changing fashion trends can easily cause production destinations to be shifted by designing countries.
For this reason, many garment workers are employed as seasonal workers or on a probation basis. They very rarely have contracts let alone long term contracts.
On the opposite end of the spectrum, when there is a lot of work, a typical workday can be between 10-16 hours for 7 days in a week. Workers are also forced to work overtime without pay for fear of losing their jobs.
Lack of social welfare
Most garment workers don’t have medical or social welfare since their employers don’t make any contributions for this.
Health and safety issues
Some of the unhealthy conditions that garment workers face include; extremely high temperatures, little or no ventilation, poor lighting, exposure to chemicals, unhygienic conditions and lack of water for drinking and sanitation
These conditions often lead to sicknesses like asthma and many complain of fatigue, fever and headaches.
Furthermore, the poor infrastructure lead to two of the deadliest garment factory disasters in 2012 and 2013 in Bangladesh: The Tazreen factory fire and Rana Plaza Factory collapse are a testament to the astounding health and safety concerns of the industry.
Harassment
Garment workers are mostly women and they face the most harassment in the workplace including verbal, physical and sexual abuse. They are often threatened with dismissal if they raise any sort of alarm.
Since women are also forced to work long hours, they also face threats (including sexual attacks and robbery) when travelling.
Empowering Workers Through Fairtrade
Fairtrade was certified in the cotton industry in 2005. Ever since, in order to address challenges in the textile and garments industry, Fairtrade has sought to expand to the rest of the textile industry supply chain.
The approach is geared towards comprehensively engaging employers and workers in the value supply chain in order to influence better working conditions and pay. Fairtrade also seeks to engage brands to commit to Fairtrade terms.
The fundamental features of the Fairtrade Textile Standard include;
1| A ‘brand commitment supply chain certification’ encourages operators, contractors and sub-contractors to be compliant to fair employment and textile industry standards.
2| Training and capacity building for workers to among other things raise their awareness about workplace rights and give workers tools to unionize. It also comprises procedures to include civil society in grievance cases.
3| Requires implementation of living wages within 6 years
4| Strict safety requirements especially for; proper handling of hazardous material, protective clothing, fire and building safety
5| Labelling using Fairtrade labelling rules
6| Product comparison and traceability
While this measure was the logical step in protection of industry workers, it is an expensive certification to purchase, consumers are not willing to pay higher costs and there are no regulating bodies imposing these standards.
Consumers are most often unaware of the real issues faced by garment workers and do not yet understand the impact of such a certification; this results in not finding value in paying the premium for the certification.
Sources:
Comentarios